In the food industry, the use of rotary and diverter valves is critical for ensuring efficient material handling while maintaining the highest hygiene standards. These components play a vital role in the safe transport of ingredients and finished products, where the risk of contamination must be minimized. The design of these valves is paramount; they must adhere to stringent sanitary requirements to facilitate effective cleaning and prevent the buildup of residues. Features that support Clean-In-Place (CIP) cleaning processes are essential, allowing for thorough sanitation without the need for disassembly. By prioritizing hygiene in their design, rotary and diverter valves help food manufacturers comply with industry regulations and ensure the safety and quality of their products.
Enhancing Quality and Safety in Food Processing Through Innovative and Reliable Solutions
Rotary and Diverter Valves for the Food Industry
Rotary and Diverter Valves Engineered for the Food Industry
Food Applications
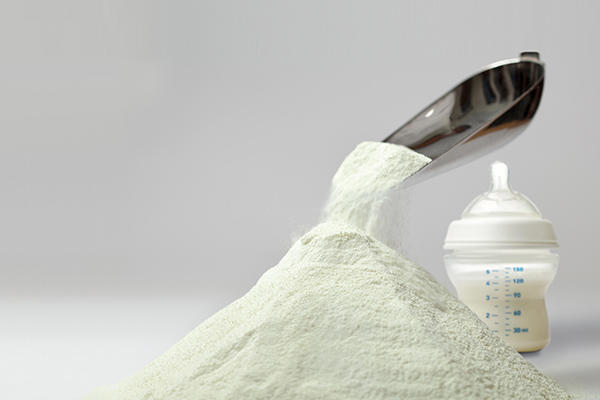
Rotary and diverter valves play a critical role in the efficient handling of dairy products, ensuring both product quality and hygiene throughout the processing stages. These valves are designed to facilitate the seamless transfer of dairy ingredients, including milk, cream, and cheese, while significantly reducing the risk of contamination. Their sanitary construction allows for easy cleaning and maintenance, which is essential for adhering to the strict hygiene standards required in dairy processing facilities. Additionally, the precise control provided by rotary and diverter valves enables accurate portioning and routing of dairy products, helping manufacturers maintain consistency and quality. By incorporating these advanced valves into dairy production systems, businesses can optimize operational efficiency and ensure compliance with food safety regulations.
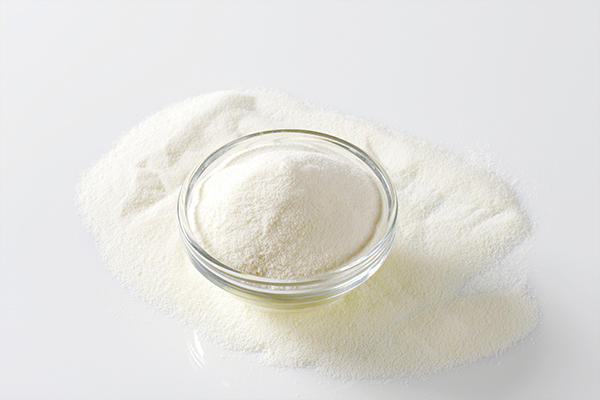
Rotary and diverter valves are vital for the effective handling of starches in food processing, where maintaining product integrity and operational efficiency is essential. These valves facilitate the smooth transfer of various starch-based ingredients, such as corn starch and potato starch, while minimizing the risk of contamination. Designed with sanitary principles in mind, rotary and diverter valves allow for easy cleaning and maintenance, which is crucial for meeting the stringent hygiene standards in starch processing environments. Their precise control capabilities enable accurate portioning and routing of starches, ensuring consistent quality in the final products. By integrating these advanced valves into starch handling systems, manufacturers can enhance productivity while adhering to food safety regulations.
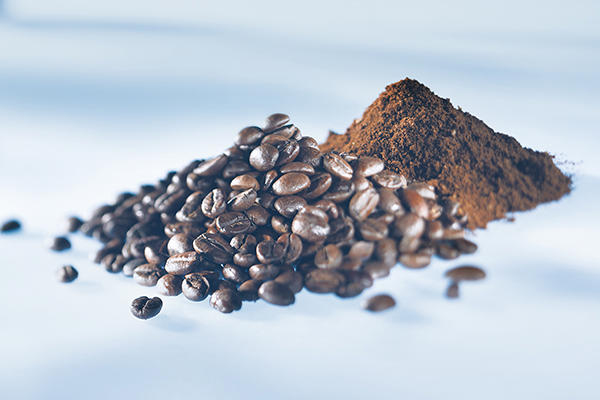
Rotary and diverter valves are crucial for the efficient handling of coffee in various stages of processing and packaging, where maintaining product quality and flavor integrity is essential. These valves facilitate the smooth transfer of coffee grounds, liquid coffee, and other coffee-based products, minimizing the risk of contamination and preserving the rich aromas and flavors that coffee lovers expect. Designed with sanitary principles, rotary and diverter valves allow for easy cleaning and maintenance, which is vital for meeting the stringent hygiene standards in coffee processing facilities. Their precise control capabilities enable accurate portioning and routing, ensuring consistency in product quality. By integrating these advanced valves into coffee handling systems, manufacturers can enhance operational efficiency while ensuring compliance with food safety regulations.
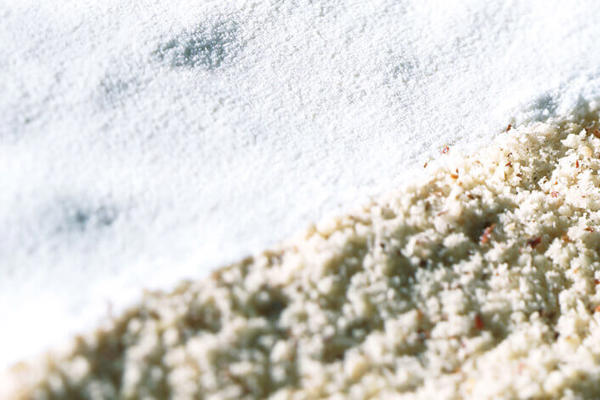
Rotary and diverter valves are integral to the efficient handling of food ingredients across various processing applications, where maintaining product quality and safety is critical. These valves facilitate the seamless transfer of a wide range of ingredients, including powders, granules, and liquids, while minimizing the risk of contamination. Engineered with sanitary design features, rotary and diverter valves ensure easy cleaning and maintenance, which is essential for adhering to the strict hygiene standards required in food processing environments. Their precise control capabilities allow for accurate portioning and routing of ingredients, ensuring consistency and quality in the final products. By incorporating these advanced valves into food ingredient handling systems, manufacturers can optimize operational efficiency while complying with food safety regulations.
Standards, Certificates & Labels
In the food processing industry, adherence to rigorous certificates, standards, and labels is essential for ensuring product safety and quality. Coperion components such as rotary and diverter valves comply with key industry regulations ensuring the high quality standards of our equipment.
-
European Hygienic Engineering and Design Group (EHEDG)
Coperion is a proactive member of the European Hygienic Engineering and Design Group (EHEDG), ensuring that the latest developments and directives are seamlessly integrated into the design of all our components.
-
USDA Certification
Coperion adheres to the rigorous regulations set by the USDA (United States Department of Agriculture) Dairy Grading Branch, which certifies our components for their sanitary and easy-to-clean designs.
-
ATEX Regulations
Coperion is committed to adhering to ATEX directives, ensuring that our components are designed and certified for use in potentially explosive atmospheres, thereby prioritizing safety and compliance in all applicable environments.
Learn more about Coperion components
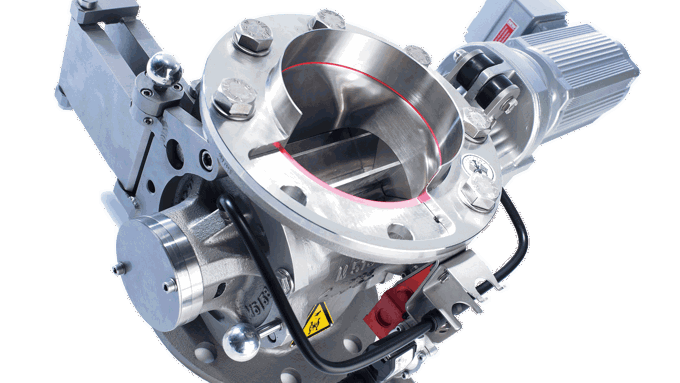
Sanitary Design
Discover how our innovative sanitary design solutions enhance hygiene and efficiency in food processing.
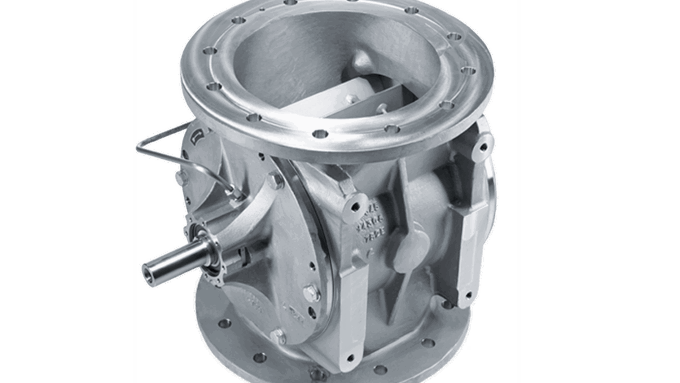
Range of Rotary Valves
Explore our comprehensive range of rotary valves designed for optimal performance and reliability.
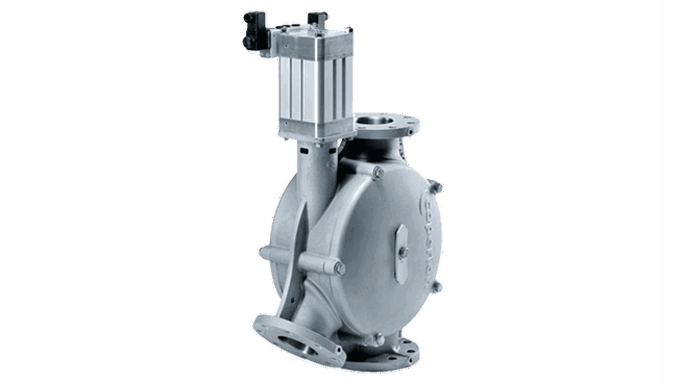
Range of Diverter Valves
Discover our extensive selection of diverter valves engineered for superior performance and versatility in diverse food applications.
Your contact for food components
-
Jochen Sprung
Head of Sales and Business Development, Coperion
- email: jochen.sprung@coperion.com
- telephone: +49 (0)751 408 584