As producer of nutrition and body care products for infants, Töpfer GmbH in Dietmannsried, Germany is obliged to extraordinary accuracy in production and packaging. The company, which, from a technological point of view, classifies itself somewhere between a dairy and pharmaceutical producer, pays highest attention to the selection of sanitary components for its process. As a result, Töpfer has been a dedicated customer of Coperion for the supply of sanitary rotary valves and diverter valves for powder conveying.
注册订阅科倍隆新闻通讯,查看我们最新动态
Experience report of Töpfer – June edition of the magazine "molkerei industrie"
Only sanitary components are used in Töpfer's production
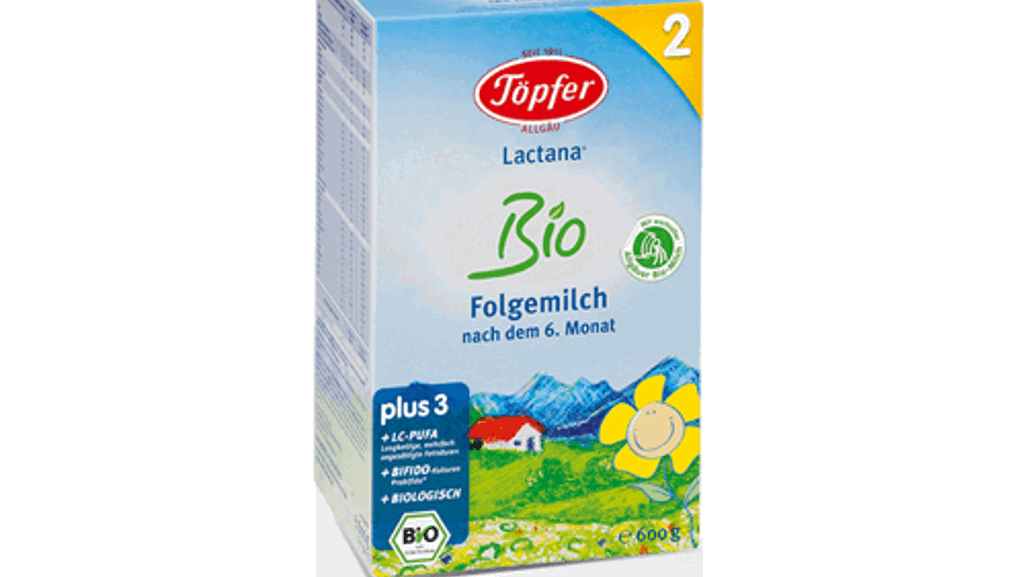
“Through a former employer, I have already been in close contact with company Waeschle, who already was leading in powder conveying technology in the materials handling industry. Therefore, it made sense, that 10 years ago we contacted their successor Coperion, to further improve our sanitary standard”, explains head of production Alfred Weixler.
At that time Töpfer bought their first sanitary rotary valve. Meanwhile five rotary valves and four diverter valves are in use in the production site at Dietmannsried. In addition, Thomas Bürkel, Managing Director and responsible for production explains that Töpfer is in the project phase for modernization. Also here, Coperion components will be installed at key areas, says Bürkel.
EHEDG-certified
Daniela Oehler, product manager at Coperion and active member in the EHEDG working team dry solids explains: “Our components are not only designed according to EHEDG guidelines, they are also EHEDG certified. This differentiates enormously between competitor products, who only adapted their design to stainless steel.
What distinguishes Coperion components, is the gap free design, especially in critical areas, such as inlet flanges or side cover gaskets. This is very important, when the production plants are cleaned wet, in order to prevent product deposits and also humidity residues in gaps.
What distinguishes Coperion components, is the gap free design, especially in critical areas, such as inlet flanges or side cover gaskets. This is very important, when the production plants are cleaned wet, in order to prevent product deposits and also humidity residues in gaps.
Andreas Sick, Head of Töpfer's Maintenance explains: “ We regularly clean dry and also wet from time to time. After each cleaning process we open the rotary valves to check if there are water residues. Until today, we never found anything. In this context, Weixler highlights the user friendliness of Coperion’s flame proof rotary valves, who can be disassembled with little effort.
Our components are not only designed according to EHEDG guidelines, they are also EHEDG certified. This differentiates enormously between competitor products, who only adapted their design to stainless steel.
Daniela Oehler , Product Manager at Coperion
Per Andreas Sick: “The rotary valves run perfectly. We haven’t been able to find a better product in the market.”
Both Töpfer employees are also satisfied with the Coperion after sales service. Weixler: “They do not only sell, but also take care of their customer afterwards”.
Jochen Sprung, Head of Sales and Business Development at Coperion summarizes this perfectly: “It is our utmost interest to keep in close contact with the users. This gives us the necessary impulses to further develop our products.
Published in the June edition of the magazine "molkerei industrie".
-
Jochen Sprung
Head of Sales and Business Development, Coperion
- email: jochen.sprung@coperion.com
- telephone: +49 (0)751 408 584