Food manufacturing facilities will typically include several pneumatic conveying types. The mode of transfer of raw ingredients or final product is dependent on many process parameters, including material characteristics, distance to be transferred, required rate of transfer, friability of product and/or segregation concerns. In the case of raw material delivery, the type of container in which the ingredient is originally received can also be a factor. For example, majors such as flour, grains, starches, and sugars are often received by truck or railcar and then stored in silos prior to usage. Pressure Differential (PD) trucks and railcars use positive pressure to unload material, whereas other types of delivery to the blending batching steps can involve either positive pressure or negative pressure. It is therefore important when choosing the conveying method that a full examination of several process parameters be completed, since different options can result in cost savings and efficiency improvements.
Positive pressure systems (see illustration below), are typically used to convey bulk materials from a single source to one or multiple destinations. This is done by use of a positive displacement blower blowing into material entry points located downstream. These entry points then meter each product into the conveying line by means of a rotary airlock valve which maintains the pressure differential between the ambient atmosphere and that of the conveying line. Material and air blown through the line exit at single or multiple use points where they are separated by means of a filter receiver or cyclone separator, or fed directly into process vessels. Positive pressure conveying systems are typically used to transport product over long distances and at high throughputs. Applications which involve pressure conveying often include loading and unloading of large volume vessels such as silos, bins, railcars, trucks, and bulk bags.
注册订阅科倍隆新闻通讯,查看我们最新动态
Food manufacturing facilities will typically include several pneumatic conveying types. The mode of transfer of raw ingredients or final product is dependent on many different process parameters. In this article we investigate the question which method is best for which application process step.
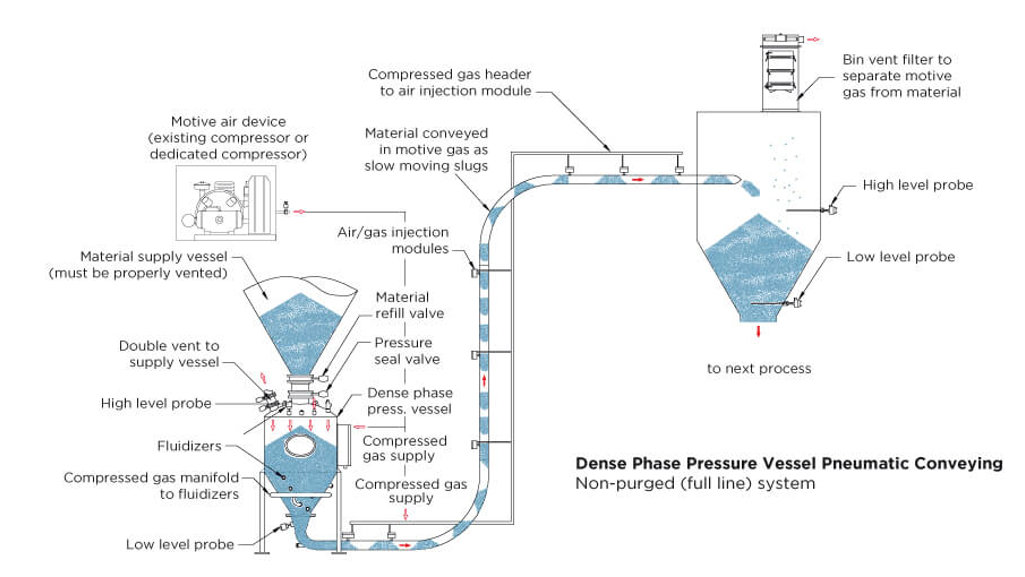
Conversely, negative pressure or vacuum systems are generally used for transporting material from multiple sources such as storage vessels, process equipment, bulk bags, trucks and railcars, to individual or multiple destinations and are used for lower volumes and shorter distances. Negative pressure is created by a positive displacement vacuum blower located at the downstream end of the system. Material can enter the system via bag dump stations equipped with rotary airlock valves, handheld pickup wands, and pickup hoppers. Material exits the system through filter receivers that separate the material from the conveying air directly above process equipment, surge hoppers, storage vessels or other discharge points. One of the advantages of vacuum systems is the inward suction created by the vacuum blower and reduction of any outward leakage of dust. This is one of the reasons why vacuum systems are often used in higher sanitary or dust containment applications. Another advantage of vacuum systems is the simple design for multiple pickup points. It should be noted, however, that the distances and throughputs possible with a vacuum system are limited due to the finite level of vacuum that can be generated.
Contact
-
Sharon Nowak
Global Business Development Manager Food & Pharma
- email: SNowak@coperionktron.com
- telephone: +1 856 256 3119
- Sharon Nowak on LinkedIn Profile