The word “dragee” is derived from the Greek word tragemata (sweetmeat, dessert) and in French it primarily means almonds coated with sugar. This traditional confectionary method utilizing sugar coating was eventually adapted to oral solid dosage (OSD) pharmaceuticals and nutraceuticals to make bitter medicines more palatable.
Sign up for the Coperion newsletter to receive the latest updates
Dragee production: everything from a single source
Positioned for the future: Coperion as a system provider in this case study of dragee production.
In traditional sugar coating methods, the gapless layer above the core often contains sugar and other excipients and is thicker than that of film-coated tablets. The outer layer of dragees may contain colorants and flavorings, while their core consists of a powder mixture, granules, or a granule-pellet mix (with a proportion of pellets typically less than or equal to 25%). The latter of the three options can be chosen if a combination of active ingredients requires separation in order not to influence the efficacy and to avoid interactions.
This multi-layer coating method generally makes dragees easier to swallow than uncoated tablets due to their smooth and polished surface. They also lock in unpleasant odors and taste, and protect the core from UV radiation, oxygen and moisture. The coating allows for controlled release of APIs, vitamins or similar in the targeted location of the body by e.g. achieving a gastric juice resistance. It can improve the appearance through the addition of colorants, which also facilitate identification and therefore drug safety. Furthermore, the coating increases mechanical stability during production, packaging and shipping.
Production of coated dragees using batch processing
The production of dragees is simple in the macro view. When dealing with powders, moist granules of mixed APIs and excipients are produced, sieved (moist), dried, sieved again, compressed and coated. In the rarer case of pellet inclusion, the dragees must be formed separately by extrusion of the moist granules and followed by spheronization before mixing with main granules.
In addition, indispensable intermediate and accompanying processes steps are utilized before the mixing stage including ingredient material handling. These steps include conveying, weighing, dispensing, dosing, and feeding. Processes such as the preparation of granulating liquid, coating solutions or, for example, a possible coating of the tablet compression chamber will also occur.
Dosing/feeding
In batch production, weighing can be carried out manually or automatically. Automation can be particularly useful on a production scale. Coperion K-Tron offers weight-regulated, gravimetric feeding for precise dosing. For batch processes, there are gain-in-weight as well as loss-in-weight solutions, depending on the parameters of the process. Today’s automated dispensaries often utilize Coperion K-Tron loss-in-weight feeders due to their extremely high accuracies. Coperion K-Tron vacuum conveying solutions ensure the automated refilling and transfer of raw materials into the feeders. Transfer of the raw ingredients can include sources such as bulk bags, drums, bags or IBC’s. The dosed raw material mixture can then be transferred to a bulk material container, or it can be fed or conveyed directly into the mixer.
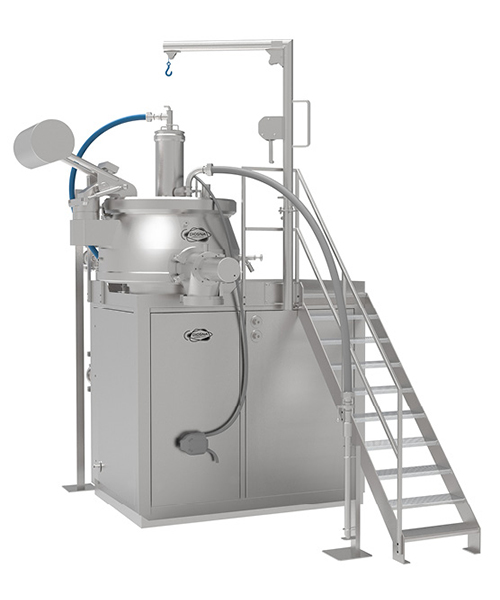
Granulation
This process step can be carried out in different ways, depending on the desired outcome. If the objective is to create a granules-based dragee core, batch granulation can be achieved using a combination of a high-shear mixer and fluid bed processor, or fluid bed granulation, or high-shear granulation in a one-pot system including vacuum drying. All three, respectively four, granulation methods are suitable to produce a granule-based dragee core. For a granule & pellet-based core not dry but moist granules are required for extrusion and spheronization. For this reason, only granulation in a high-shear mixer can be considered (all other methods mentioned include drying).
DIOSNA offers all of these options. High-shear mixing and granulation technology produces granules of remarkably high homogeneity and quality in a matter of minutes supported by the specific conical-cylindrical architecture of the DIOSNA’s P-line vessels and their two mixing tools.
Wet granulation is initiated by adding the granulating solution and completed by reaching the determined end points which can be simply or very specifically. A basic feature of a DIOSNA High-Shear granulators is comprised of software and a variety of measuring parameters. The validated program is capable of calculating a range of data and key figures derived from the measured values like temperature, peripheral speed of the mixing tool, Froude number (needed for scale-ups), active power, total energy consumption, torque, power curve inflection point. Should the adjustable maximum values are for power and torque be exceeded, warnings or alarms are triggered, thereby advancing the mixing program.
Followed by this process prior drying the moist granulate is wet-sieved. For sizing the wet mass specified intermediate equipment such as the Kemutec Conemill generates a homogeneous mass of granules which then can be conveyed to a fluidized bed dryer (either directly or via a bulk container). This helps to uniform granules in size and thereby increasing the overall surface area, thus reducing the subsequent drying time.
Segregation
Subsequent to the drying process the next intermediate step is to de-agglomerate the lumps of the dry granulate e.g. by the previously mentioned cone mill prior passing it to a free-fall mixer or tumbler for final mixing before pressing.
Pressing the dragee core
Finally, the granulate is transferred to an IBC. If allowed by the ceiling height of the production side, the IBC can be placed on top of a feed device, which is used to supply the tablet press. If the height for this is not available, the IBC contents can be conveyed using Coperion pneumatic conveyors directly to the feed frame of the tablet press.
Coating
The pressed cores will be released in a container and transported to a coater. Gabler provides un-perforated, onion shaped pan coaters. The application of the coating solution occurs by means of a high-pressure spray system, resulting in precise dosing of the application solution. Supply air is conditioned, and air volumes reach approx. 1200m3/h.
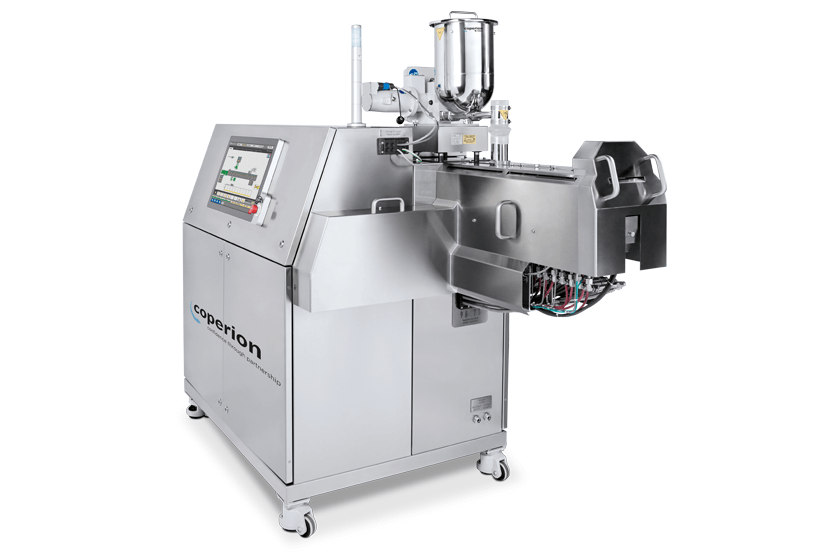
Semi-continuous processing
There is a range of options for dragee production. Besides the former described batch process there are also semi-continuous solutions. Coperion,Gabler, and Mucon also offer solutions for continuous and semi-continuous production. The gravimetric loss-in-weight feeders, the vibratory feeders, as well as continuous pneumatic conveying including receivers, valves etc., are globally used for continuous applications.
Furthermore, Coperion provides continuous hot-melt extrusion and wet extrusion. Hot-melt extrusion allows for a solvent-free production of solid dispersions or solids solutions of APIs (also BCS class 2 & 4), thus enhancing their bioavailability. This presents a particular advantage for APIs whose crystalline structure previously made this difficult. After extrusion the wet mixture is milled and cooled before pressing.
Coperion Food, Health and Nutrition Divison
With its own brands, the Coperion Food, Health and Nutrition Division can cover around 85% of the entire production chain for the manufacture of dragees using the batch process.
A number of systems, conveying equipment and software are required to build the processes. For adequate and efficient planning, installation, commissioning and, in particular, subsequent production (or development), it is decidedly advantageous to implement equipment that is as coordinated as possible and to ensure processing and service from a single source.
With the fusion of the brands Coperion, DIOSNA, Gabler, Kemutec, Mucon and VMI, a strong group of equipment and systems manufacturers have emerged. This allows the Coperion group to provide the perfect combination of integrated processes for batch, continuous or semi-continuous dragee production.
Your Contact
-
-
Sharon Nowak
Global Business Development Manager Food & Pharma
- email: SNowak@coperionktron.com
- telephone: +1 856 256 3119
- Sharon Nowak on LinkedIn Profile