As a manufacturer of high-class twin screw extruders, Coperion has decades of experience with compounding processes in cable production and provides the right machines and solutions for your needs. Learn more in the following infographic.
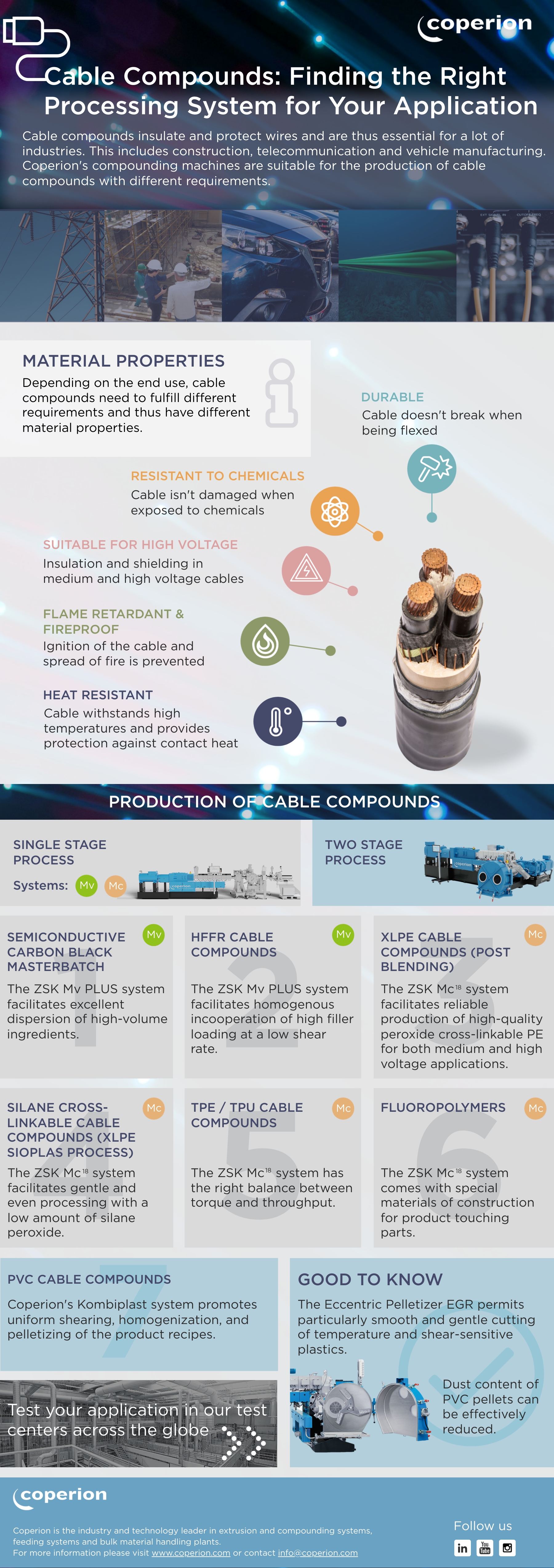
Depending on the end use of the cable, compounds need to have different material properties. A simple recharger; for example, does not have to comply with the same standards as a cable used for robotics in an industrial context, on a vessel, or even under water. In this connection, the quality requirements of the insulation material are not only determined by the general safety level but also by the environment in which the cables are used. Some cables are exposed to high voltages, extreme heat, and even chemicals which is why they need to be especially sturdy. Typical material requirements towards cables are as follows:
- Durable: The cable doesn’t break when being flexed.
- Resistant to chemicals: The cable doesn’t get porous when exposed to chemicals.
- Suitable for high voltage: The cable is able to insulate and shield the wires in medium and high voltage applications.
- Flame retardant and fireproof: The cable cannot be ignited and doesn’t spread fire.
- Heat resistant: The cable withstands high temperatures and protects against contact heat.
To achieve the desired characteristics and product quality, the recipe as well as the compounding process need to be individually adapted to the application. Coperion offers both a single and a two-stage process based on its proven ZSK twin screw extrusion technology. The single stage process is highly suitable for the production of semiconductive carbon black masterbatch, HFFR, XLPE, Silane crosslinkable cable compounds (XLPE Sioplas process), TPE/ TPU and fluoropolymers. Depending on the process, Coperion normally recommends our high-performance ZSK Mc18 or ZSK Mv PLUS extruder. The latter facilitates excellent dispersion of even high-volume ingredients which are commonly used in a number of cable recipes. Both systems are highly efficient, gentle and make optimal homogenization and incorporation of fillers possible. In addition, we offer further machine types and even lower-cost options, if the application allows it.
When it comes to the production of PVC cable compounds Coperion provides a reliable two-stage process. The Kombiplast system consists of a ZSK twin screw extruder and an ES-A single screw discharge which safeguards gentle pressure build-up of shear-sensitive products. This set-up is known for its very uniform shearing, homogenization, and pelletizing capabilities and is therefore the ideal solution for the production of PVC. To promote particularly smooth and gentle cutting of temperature and shear-sensitive plastics our experts also recommend using Coperion’s Eccentric Pelletizer EGR. Thanks to the EGR knife's special metal alloy and design as well as the system’s unique knife rotor and knife combination, the proportion of fines can be almost completely prevented which helps to avoid contamination and reduces cleaning times.
Download the Infographic
Learn more about Coperion's Solutions
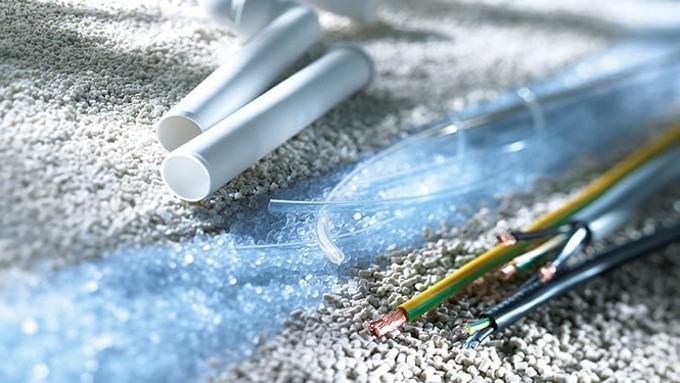
Manufacturing of Cable Compounds
Our technologies have long proven themselves in the compounding of a wide variety of cable applications. We realize solutions for all production steps – from material handling and feeding, to dryblend production, compounding, and pellet cooling, to storage and filling.
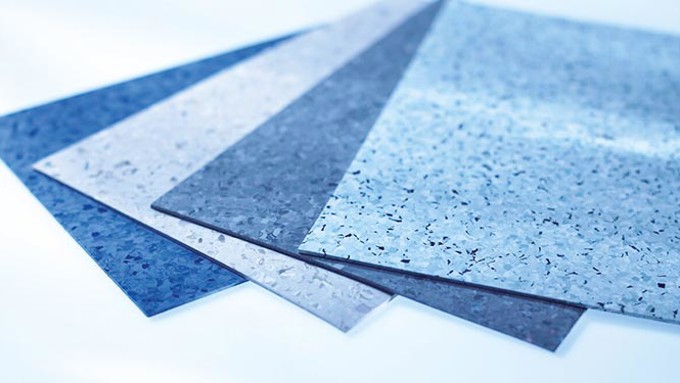
Efficient PVC Processing
The production of high-quality end products is the key to success when meeting the high demands of the PVC market. Coperion and Coperion K-Tron are specialists in the design, construction and implementation of complete plants and systems for processing of PVC.
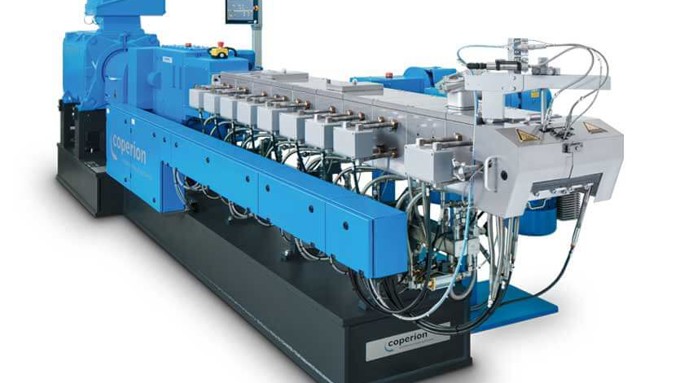
Extruders & Compounding Machines
As a pioneer in the development of the closely intermeshing, co-rotating twin screw extruder, we possess a unique know-how and an extraordinary wealth of experience in this field.