Most Coperion K-Tron feeders have generally been supplied with DC motors in nearly all of our applications. As a result of technological advances in the industry and higher availability of motors we now offer most feeder models with servo motors. This type of motor technology combines the strengths of AC and DC motors and is ideal for any kind of feeding solution. Learn more about the reasons for the switch as well as the long-term benefits in the following infographic:
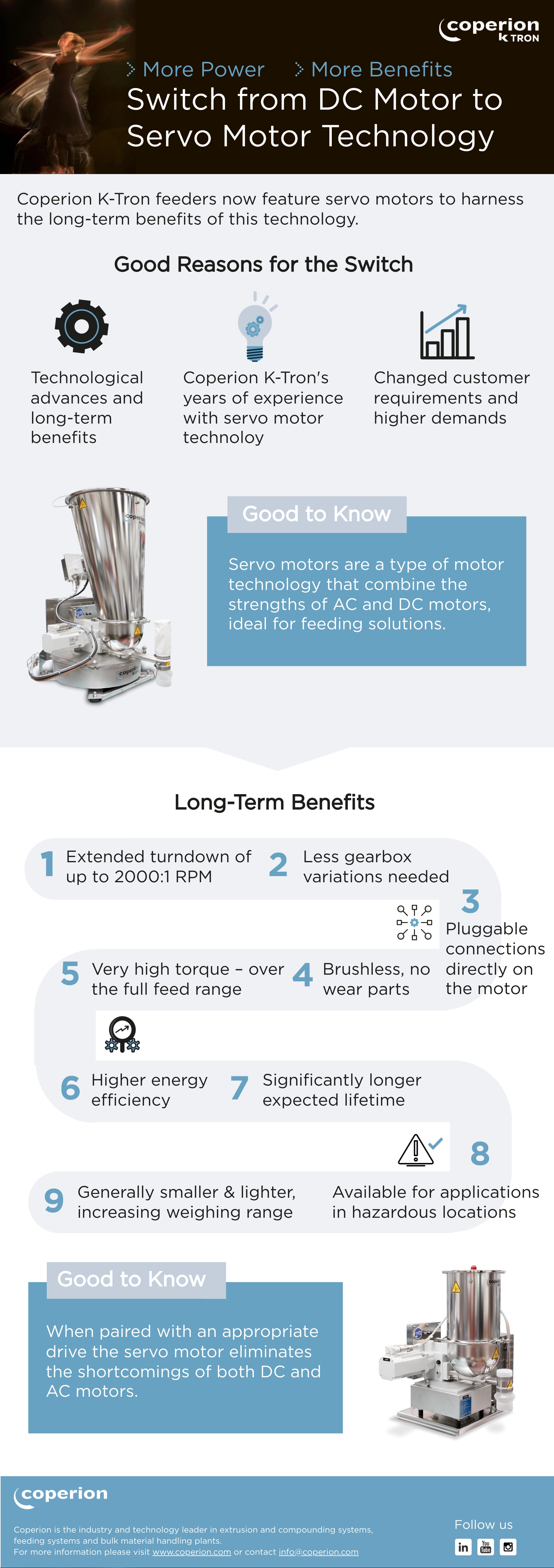
After evaluating the market situation over many years, our feeder experts from Coperion K-Tron haven taken the decision to switch from DC to servo motors for three main reasons. Firstly, the industry has undergone a variety of technological advances in recent years, with servo technology becoming more and more prominent. We recognized that the benefits of servo motors made them ideal for feeding applications. Secondly, we have already accumulated years of experience with servo technology. We have not only successfully implemented this technology in the K3 Pharma feeder line, but we have also built other feeders with servo motors in a variety of applications upon customer request. This also leads to the third reason, namely changing customer requirements and a higher demand.
Long-term Benefits of Servo Motors in Feeding Applications
Servo motor technology comes with many long-term benefits in feeding applications compared to DC motors. Due to the control that can be achieved given the synchronous nature of their operation, servo motors are capable of tremendous turndown (up to 2000:1 RPM) without overheating or loss of torque. As a result, it will no longer be necessary to offer multiple gearboxes to cover the full feed range of a feeder, making the implementation of a single feeder configuration more flexible in its application. Since servo motors are smaller and lighter, they facilitate an increase in weighing range. It also allows for pluggable connections directly on the motor, which makes dis- and reassembly much easier. Furthermore, it is brushless and has no wear parts which is beneficial from a maintenance perspective. Since it has no brushes – and therefore does not generate internal arcs/sparks – hazardous locations do not pose a barrier. In addition, servo motors tend to be a lot more energy-efficient which helps to cut overall operational costs. All these advantages contribute to a significantly higher expected lifetime.
In a nutshell, servo motors present the best-case scenario for operating feeders. Their high turndown capability can minimize the need for feeder configuration changes such as screws, tubes, and gear ratios over a wide range of feed rates and bulk materials. Our service teams offer modernization packages for customers with Coperion K-Tron gravimetric feeders equipped with DC or AC motors who would like to make the switch to servo motors.
Download the Infographic
Learn more about Coperion K-Tron's Feeding Equipment
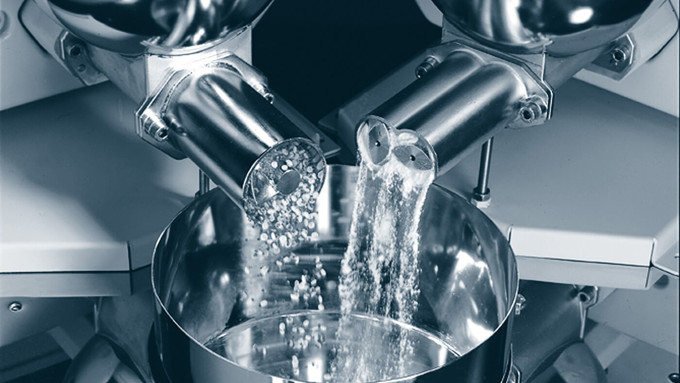
Smart Feeding Solutions
From screw feeders to vibratory feeders, bulk solids pumps, weigh belts, liquid feeders and flow meters, all Coperion K-Tron feeders are offered in a variety of configurations, which can be combined to create an optimal solution for any application.
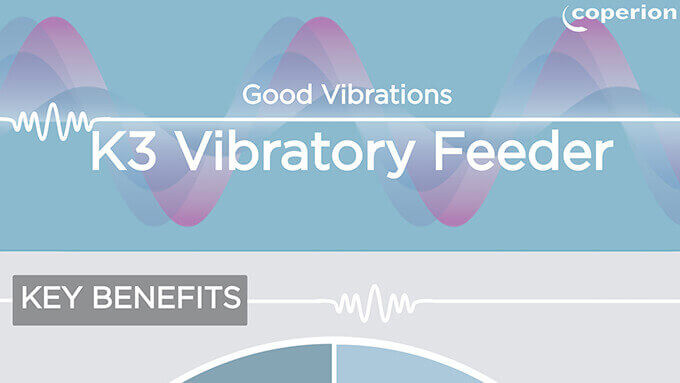
Vibratory Feeder|Infographic
Thanks to their free-flowing mode of operation, vibratory feeders are especially suitable for hard-to-handle and non-homogeneous bulk materials. The unique Coperion K-Tron K3 Vibratory Feeder is based on a new pendulum technology and offers a highly accurate and reliable feeding solution for many bulk solids.
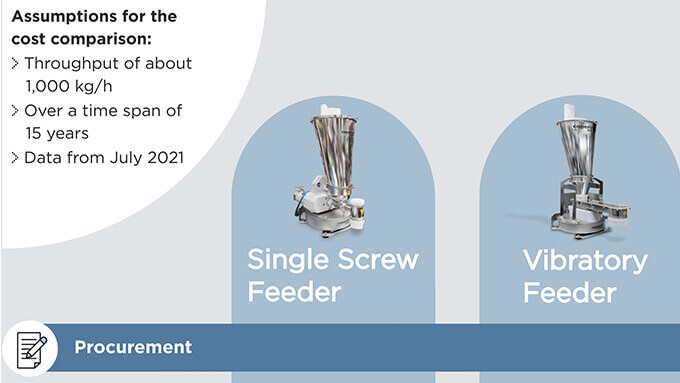
Comparing Total Life Cycle Costs|Infographic
In many applications Loss-in-weight (LIW) feeders are the equipment of choice in order to achieve high accuracies, fast batching and a high level of control. As part of the decision-making process plant managers usually have the freedom to choose between various LIW systems.