Color masterbatches are solid concentrated color additives that are commonly used in many plastics processes. If their quality is right, they are reliable, easy to handle, and usually more cost-effective than applying raw pigments. To achieve high-value masterbatches while keeping manufacturing costs manageable, Coperion has composed a complete and field-proven solution with a good price-performance ratio. This comprehensive package consists of an STS compounder and an S60 volumetric feeder. Learn more about the prerequisites of color masterbatch production and how our system is designed to meet these requirements.
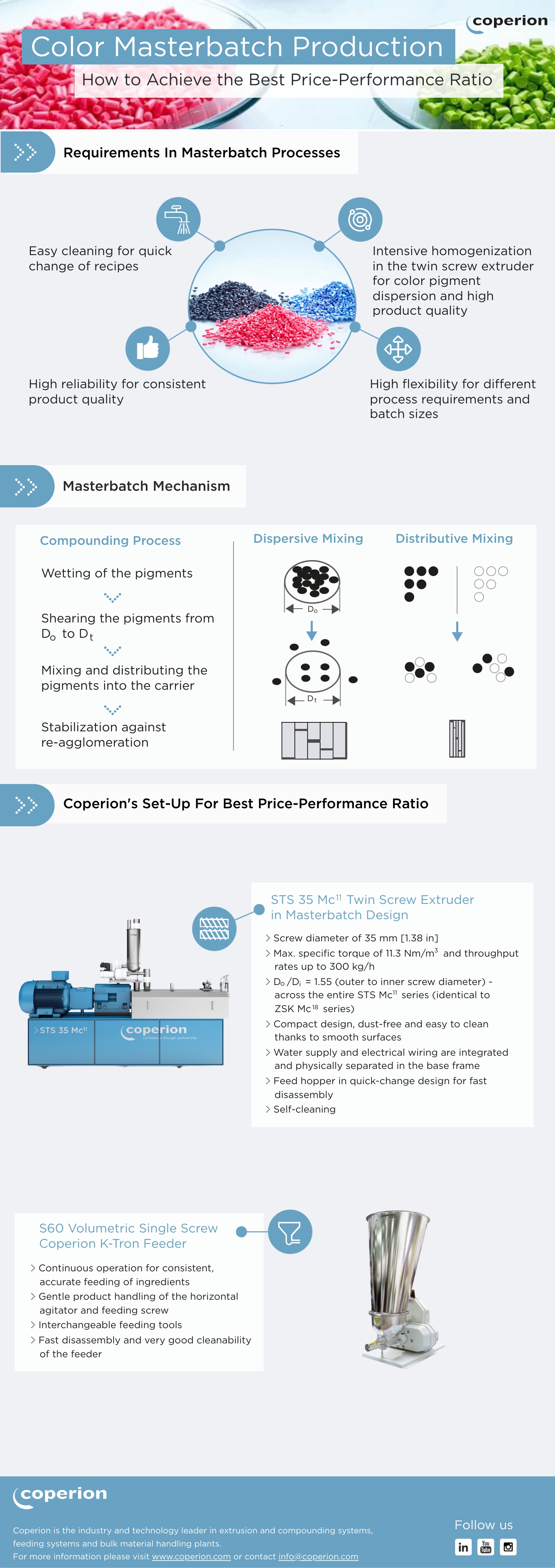
Generally, manufacturers of color masterbatches have very specific requirements in terms of process reliability, productivity and flexibility. They do not only have to cater to frequent recipe and color changes but also maintain a consistent product quality. To ensure reliable color pigment dispersion and avoid agglomerates, intensive homogenization in the twin screw extruder is indispensable. In addition, the extrusion system needs to be customizable and fulfill different process requirements (e.g. premix vs. split feed) as well as adjust to varying batch sizes.
Having understood the overall requirements from a manufacturer’s perspective, we should now get a basic understanding of the masterbatch mechanism.
Mechanism of color masterbatch production
When producing color masterbatches in a twin screw extruder, the pigments are incorporated into the polymer carrier by dispersive and distributive mixing. Dispersive mixing breaks up pigment aggregates, while distributive mixing generates spatial and even distribution of the pigments. The compounding process works as follows:
Firstly, the pigment needs to be wetted with the polymer. Afterward, the pigment aggregates are sheared from a bigger size to the individual pigment size using dispersive mixing. These smaller particles are then properly mixed and distributed in the carrier matrix using dispersive mixing.
Benefit from a complete package
With this general principle in mind and decades of experience, Coperion has constantly optimized its system for the production of color masterbatches resulting in our proven package. The STS compounder, the heart of the process, comes with a screw diameter of 35 mm [1.38 in]. With its maximum specific torque of 11.3 Nm/m³ it achieves throughput rates of up to 300 kg/h. Furthermore, the diameter ratio Do/Di, meaning the outer to inner screw diameter, is 1.55 across the entire STS Mc series giving us the best shear-to-free volume ratio. This is identical to the ZSK Mc series and contributes, besides the screw design, to achieve a low filter pressure value and therefore a proper dispersion of the pigments. In addition, the twin screw features a closely intermeshing system, resulting in self-cleaning properties of the screw and barrel. The overall design of the extruder is compact, dust-free and easy to clean thanks to its smooth surfaces. Both water supply and electrical wiring are integrated and physically separated in the base frame. The feed hopper comes with quick-change design features to ensure fast disassembly for easy cleaning and fast recipe changeover.
To complement our STS extruder, our experts have access to a wide range of Coperion K-Tron feeders for every possible application or requirement. Our proven color masterbatch package comes with the S60 volumetric feeding system which ensures continuous operation for consistent, accurate feeding of ingredients. It is known for its gentle product handling of the horizontal agitator and feeding screw. Furthermore, it is designed with interchangeable feeding tools and is optimized for fast disassembly and very good cleanability of the feeder.
Download the Infographic
Learn more about Coperion's Compounding solutions
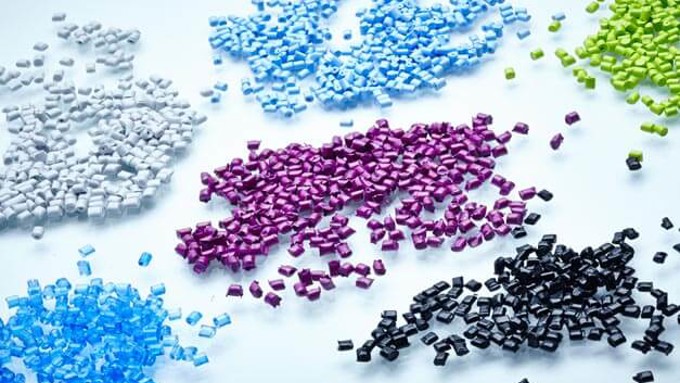
Processing of Masterbatch
Coperion compounding systems and extruders are particularly suitable for the processing of masterbatch because of their excellent mixing properties and gentle product handling.
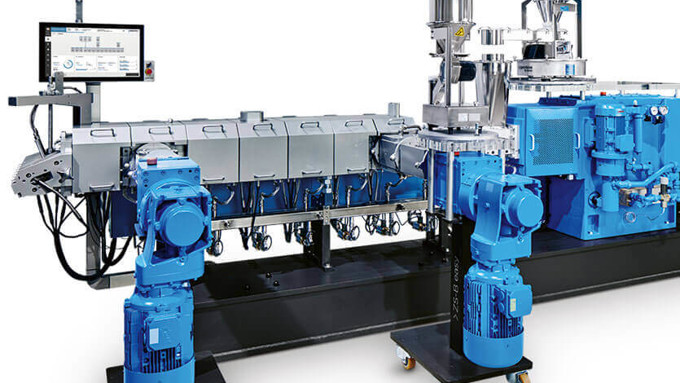
ZSK Mc¹⁸ Twin Screw Extruder
The ZSK Mc¹⁸ twin screw extruder ensures production with maximum economic efficiency.
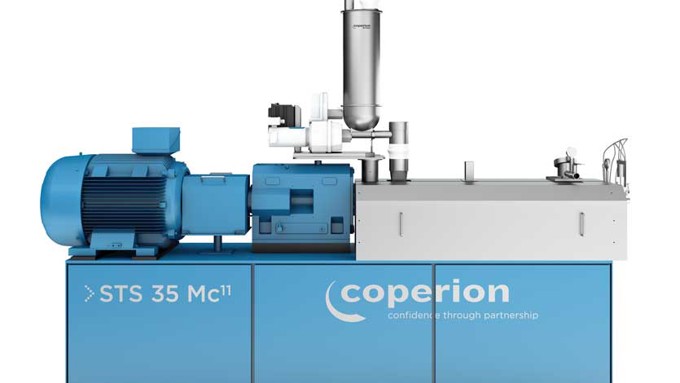
STS Mc¹¹ Compounder
The STS Mc¹¹ compounder covers most standard applications in process technology. It offers high productivity at an attractive price-performance ratio.